Friday, October 29, 2004
Discussion with Robert Lazzarini: Part 2 of 5
Today we continue the discussion with Robert Lazzarini, focusing on the process he uses for creating his distorted sculptures of common objects. (The previous installment of the discussion is available here.)
Help me understand what happens between a couple of those steps. You’re working 2-D in Photoshop doing some distortion. You take the 3-D geometry of the object into the computer, and then do you try to reproduce the distortion you’ve made in 2-D in three dimensions?
Basically. But it becomes more complex by virtue of the fact that I’m no longer dealing with X-Y coordinates. I’m dealing with X-Y-Z coordinates. Now, dealing with geometry that occupies space, or that’s projected into space instead of a distortion that’s just linear, is much more complex. I approximate what I’ve achieved in the 2-D distortion, but it needs to go beyond that in its complexity.
So the Photoshop work is more of a sketch for what you eventually make.
Exactly. Also there’s something much more immediate about it. If I’m dealing with a series, I can do hundreds of designs. And that allows me to get a lot closer to where I’m heading with a particular image than if I was dealing directly with 3-D right from the start.
Once you’ve got the 3-D coordinates in the computer and you’ve distorted those in virtual space, how do you make the transition back to a physical space?
The process I use is called rapid prototyping or computer generated model-making. I work with different service bureaus that create physical models based on 3-D data. Some are reductive processes and others are additive processes. They either mill away at a block of material or they build it line by line in successive passes to create a geometry.
And then how do you fabricate the object once you have the prototype complete?
Every object is different, and each object is a new material. Even when it’s the same material, it’s a different handling of it. They all have their complexities. With table, notebook, and pencil, some of the parts are milled but some of the parts are clamped-over tool parts which are rigid mold parts. I’m using a product called Compwood where they actually compress the wood so that the atoms fold over to give the wood a certain plasticity.
How do you find fabricators to work with all the different materials you use?
It’s an ongoing pursuit. And sometimes there are quite a few. In the case of payphone, I worked with about 45 different fabricators—from chromers and acid engravers to graphic designers, silk screeners, metal workers of varying types, anodizers, and a host of other people.
What’s that relationship like? When I think of industrial fabrication, I think of Donald Judd. He had his people who knew his vision, and they were able to execute.
It would be incredible to have a group of people realizing your vision. I’m not at that point. At the moment I have to be very hands on, from production to final finish.
But could you even work within that model if you’re using so many different fabricators for so many different kinds of materials?
Well, the thing to do is to have a studio manager who is so facile with such a range of materials and fabrication that he or she is able to access whatever specialties are needed at any given moment. But right now I need to understand all those things myself.
Are you the one who puts all these components together at the end?
Yes. In many cases that’s the essence of it because I’m getting different parts made at different places. On something like payphone, I’ll work with someone specifically on the connectivity of those parts, but those are things that I’m overseeing. Although I would like to, I never hand something over to someone and ask them to take care of it based on a set of drawings. Inevitably, things come back to the studio to be finished. That is that handmade aspect of the process.
In the next installment, we take a close look at one of Lazzarini’s skulls to see exactly how the specific distortions were made.
Help me understand what happens between a couple of those steps. You’re working 2-D in Photoshop doing some distortion. You take the 3-D geometry of the object into the computer, and then do you try to reproduce the distortion you’ve made in 2-D in three dimensions?
Basically. But it becomes more complex by virtue of the fact that I’m no longer dealing with X-Y coordinates. I’m dealing with X-Y-Z coordinates. Now, dealing with geometry that occupies space, or that’s projected into space instead of a distortion that’s just linear, is much more complex. I approximate what I’ve achieved in the 2-D distortion, but it needs to go beyond that in its complexity.
So the Photoshop work is more of a sketch for what you eventually make.
Exactly. Also there’s something much more immediate about it. If I’m dealing with a series, I can do hundreds of designs. And that allows me to get a lot closer to where I’m heading with a particular image than if I was dealing directly with 3-D right from the start.
Once you’ve got the 3-D coordinates in the computer and you’ve distorted those in virtual space, how do you make the transition back to a physical space?
The process I use is called rapid prototyping or computer generated model-making. I work with different service bureaus that create physical models based on 3-D data. Some are reductive processes and others are additive processes. They either mill away at a block of material or they build it line by line in successive passes to create a geometry.
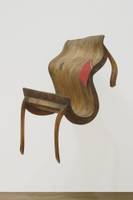
Every object is different, and each object is a new material. Even when it’s the same material, it’s a different handling of it. They all have their complexities. With table, notebook, and pencil, some of the parts are milled but some of the parts are clamped-over tool parts which are rigid mold parts. I’m using a product called Compwood where they actually compress the wood so that the atoms fold over to give the wood a certain plasticity.
How do you find fabricators to work with all the different materials you use?
It’s an ongoing pursuit. And sometimes there are quite a few. In the case of payphone, I worked with about 45 different fabricators—from chromers and acid engravers to graphic designers, silk screeners, metal workers of varying types, anodizers, and a host of other people.
What’s that relationship like? When I think of industrial fabrication, I think of Donald Judd. He had his people who knew his vision, and they were able to execute.
It would be incredible to have a group of people realizing your vision. I’m not at that point. At the moment I have to be very hands on, from production to final finish.
But could you even work within that model if you’re using so many different fabricators for so many different kinds of materials?
Well, the thing to do is to have a studio manager who is so facile with such a range of materials and fabrication that he or she is able to access whatever specialties are needed at any given moment. But right now I need to understand all those things myself.
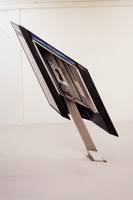
Yes. In many cases that’s the essence of it because I’m getting different parts made at different places. On something like payphone, I’ll work with someone specifically on the connectivity of those parts, but those are things that I’m overseeing. Although I would like to, I never hand something over to someone and ask them to take care of it based on a set of drawings. Inevitably, things come back to the studio to be finished. That is that handmade aspect of the process.
In the next installment, we take a close look at one of Lazzarini’s skulls to see exactly how the specific distortions were made.